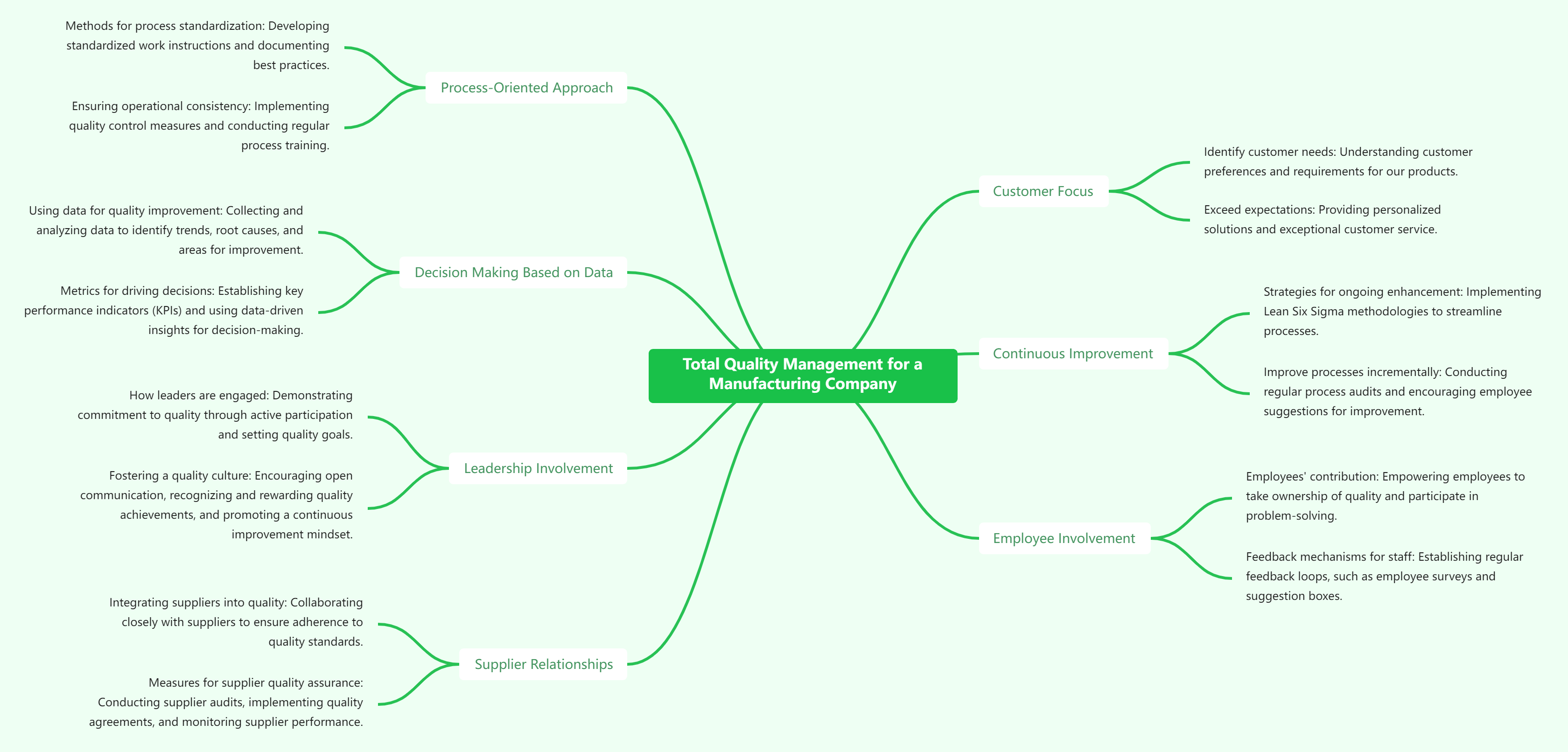
Description of the Mind Map Content
This mind map outlines the principles and strategies of Total Quality Management (TQM) specifically tailored for a manufacturing company. The key areas of focus include a Process-Oriented Approach, Customer Focus, Decision Making Based on Data, Continuous Improvement, Leadership Involvement, Employee Involvement, and Supplier Relationships.
- Process-Oriented Approach: The map emphasizes methods for process standardization, operational consistency, and the importance of developing standardized work instructions.
- Customer Focus: It delves into understanding customer needs, exceeding expectations through personalized solutions, and delivering exceptional customer service.
- Decision Making Based on Data: This section underscores the significance of using data for quality improvement, including the collection, analysis, and application of data to identify trends and areas for enhancement.
- Continuous Improvement: Strategies for ongoing enhancement are discussed, with a focus on implementing Lean Six Sigma methodologies and conducting regular process audits.
- Leadership Involvement: The map highlights how leaders engage in demonstrating commitment to quality through active participation, goal-setting, and fostering a quality culture.
- Employee Involvement: The role of employees in contributing to quality is emphasized, along with feedback mechanisms such as surveys and suggestion boxes to encourage active participation.
- Supplier Relationships: Integrating suppliers into the quality process is explored, with measures such as collaboration, supplier audits, quality agreements, and performance monitoring.
Insights from the Mind Map:
- Holistic Quality Management: The mind map suggests a comprehensive approach to quality management, encompassing various aspects from process standardization to supplier relationships.
- Data-Driven Decision Making: The emphasis on using data for decision-making underscores the importance of objective analysis and continuous improvement based on measurable metrics.
- Cultural Integration: The involvement of both leadership and employees in fostering a quality culture indicates the need for a holistic and collaborative approach to quality management.
- Supplier Collaboration: The inclusion of supplier relationships in quality measures reflects an awareness of the interconnectedness of the supply chain and the impact of supplier performance on overall quality.
Exploring Collaborative Visualization with Visual Paradigm Smart Board
Visual Paradigm Smart Board emerges as a versatile online mind map tool, seamlessly combining the functionalities of a mind map app and a collaborative brainstorming tool. Designed for intuitive use, it serves as a comprehensive mind map maker, facilitating the creation of visually engaging diagrams that outline complex concepts, strategies, or processes. Beyond its role as a mind map tool, it excels as an online brainstorming platform, promoting teamwork and idea generation. The software’s user-friendly interface empowers individuals and teams to craft intricate mind maps, fostering a dynamic environment for ideation and strategy development. Visual Paradigm Smart Board stands out as an accessible and effective online mind map software, providing a conducive space for collaborative thinking and innovation without compromising on simplicity and usability.